- Carrier Zephyr 30s Service Manual
- Carrier Zephyr 30s Repair Manual
- Carrier Zephyr 30s Repair Manual Download
- Carrier Zephyr 30s Repair Manual Pdf
File Name: | carrier transicold zephyr 30s service manual.pdf |
Size: | 4214 KB |
Type: | PDF, ePub, eBook, fb2, mobi, txt, doc, rtf, djvu |
Category: | Book |
Uploaded | 3 May 2019, 14:19 PM |
Interface | English |
Rating | 4.6/5 from 610 votes |
Status | AVAILABLE |
Last checked | 9 Minutes ago! |
View & download of more than 11939 Graco PDF user manuals, service manuals, operating guides. Paint Sprayer, Water Pump user manuals, operating guides & specifications. Zephyr AK1100S 30 Inch Under Cabinet Range Hood with 3-Speed/250 CFM Blower, Mechanical Slide Controls, Halogen Lighting, Aluminum Mesh Filters, Low-Profile Body, Multiple Color Options, Value Driven, and UL Listed: Stainless Steel. Carrier Zephyr 30s Manual PDF online, free is full of good knowledge and reference. It makes the readers have good and much knowledge. It makes the readers have good and much knowledge. Reading Carrier Zephyr 30s Manual PDF online, free can be disappeared the readers stress with the daily routine. Manuals of Carrier's Hi-Walls, Ducted, Controllers and also Cassettes. Call 13 Cool (13 2665) For Carrier chillers, air handling units and service please call 1300 130 750.
carrier transicold zephyr 30s service manual
TABLE OF CONTENTS (Continued)Figure 1-5 Typical Standby Control Box. Figure 4-5 Typical Setup For Testing Pressure Switches HP1 And HP2. Figure 6-1 Electrical Schematic Wiring Diagram - Based On Dwg. No. 62-61350 Rev D. Figure 6-2 Electrical Schematic Wiring Diagram - Based On Dwg. No. 62-61350 Rev D. Figure 6-3 Electrical Schematic Wiring Diagram - Based On Dwg. No. 62-61353 Rev A. Figure 6-4 Electrical Schematic Wiring Diagram - Based On Dwg. No. 62-61354 Rev A. Figure 6-5 Electrical Schematic Wiring Diagram - Based On Dwg. No. 62-61354 Rev A. Figure 6-6 Electrical Schematic Wiring Diagram - Based On Dwg. No. 62-61352 Rev A. PageTable 1-2. Table 2-1. Table 2-2. Table 4-1. Table 4-2. Table 4-4. Table 5-1. Table 5-2PageDuring normalDuring all pre-trip inspections, daily inspections,Stay clear of all moving parts when the unit is inAlways obtain first aid or medical attention immediately.Wear hearing protection as required. Keep hands, clothing and tools clear of the evaporator and condenser fans. No work should be performed on the unit until all circuit breakers are turned off, and battery power supply isAlways work in pairs. Never work on the equipment alone. In case of severe vibration or unusual noise, stop the unit and investigate.This unit is equipped with Auto--Start in both the road and standby modes. The unit may start at any time. When performing any check of the system make certain all circuit breakers are turnedBe sure power is turned off before working on motors, controllers, solenoid valves and electrical control switches. TagDo not bypass any electrical safety devices, e.g. bridging an overload, or using any sort of jumper wires. Problems withWhen performing any arc welding on the unit or container, disconnect all wire harness connectors from theIn case of electrical fire, open circuit switch and extinguish with CO2 (never use water).Safety--1DANGER -- means an immediate hazard which WILL result in severe personal injury or death.
- carrier transicold zephyr 30s service manual, 1.0, carrier transicold zephyr 30s service manual.
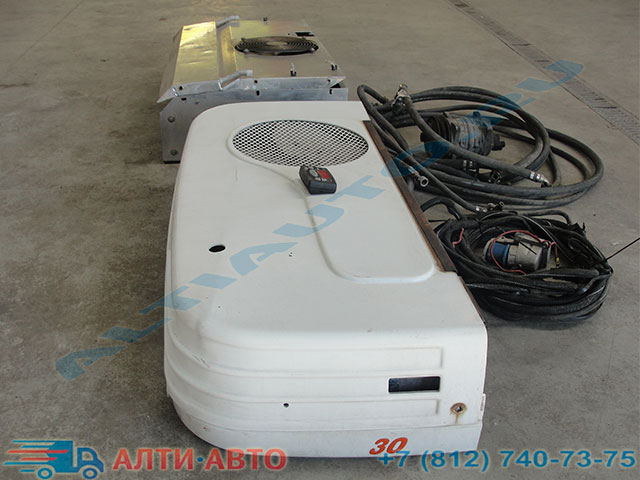
WARNING -- means to warn against hazards or unsafe conditions which COULD result in severe personal injury orCAUTION -- means to warn against potential hazard or unsafe practice which could result in minor personal injury,The statements listed below are applicable to the refrigeration unit and appear elsewhere in this manual. TheseThe unit may cycle the fans and operating compressorPress OFF key on the cab command and disconnectAlso check battery cable routing to ensure that clamps are secureCab Command) and external power circuit breaker is open.Do not use oxygen in or near a refrigerant system as an explosion may occur.Should a problem develop with these components, contact your nearest Carrier TransicoldR134A and POE oil. For more information see Technical Procedure 98-50553-00 -- Inert Gas. Brazing.Place all parts in the enclosing tube inMicroprocessor components operate at different voltage levels and at extremely low current levels. Improper use of voltmeters, jumper wires, continuity testers, etc.In certain cases, the human body can have enough static electricity to cause resultant damage to theUse proper board handling techniques. (See Section 4.17). Safety--3Press OFF key on the. Cab Command and disconnect power plug. This manual contains Operating Data, Electrical DataModel 30S truck refrigeration units listed in Table 1-1. Additional support manuals are listed in Table 1-2. The condensing section (see Figure 1-2) contains theThe condenser is of the tube and fin type and acts as aAir movement over the condenser is provided by aRefrigerant leaving the receiver is passed through the. The unit (Figure 1-1) is of the split system type with theD Road operation: the road compressor is located inThe drier is a cylindrical shell containing a drying agentTable 1-1 Model Chart. R134a. Model No. DescriptionRoad. Compressor. Standby. Condenser Weight. Road and. Road. Evap. Wt.Kg). Table 1-2. Additional Support Manuals. Manual NumberSupra 30S. Supra 30S.
Supra 30SParts List. Easy To Run. Operator’s ManualCondenser Coil. Transformer (TR). Oil Separator. Standby Motor. Standby Compressor (See Table 1-1). Control Box. Filter Drier. Liquid Line Check ValveReceiver. Discharge Manifold. Hot Gas Solenoid Valve (HGS1). Condenser Pressure Control Switch (HP2). Frame. High Pressure Switch (HP1). Condenser Pressure Control Valve (HGS2). Figure 1-2 Top ViewExpansion Valve (TXV)Quench Valve (BPV)Defrost Termination Thermostat (DTT). Figure 1-3 Rear View EvaporatorThe condenser pressure control valve (or condenser. The oil separator is installed in the discharge line fromIn the cool mode, heat isWith the solenoid coil energized,The pressure is such that refrigerantAn overload and short cycleFigure 1-4 Oil SeparatorHGS1 is normally closed and prevents discharge gasThe valve opens to allowHP1 is a normally closed switch which monitors theHP2 is a normally open switch which closes to signal theFor HP2 settings see Section 1.6.2.The thermostatic expansion valve is an automatic device which controls the flow of liquid to the evaporatorThe thermal expansion valveSection 1.6.2. To adjust the TXV, refer to Section 4.15.2.The CPR valve is installed on the suction line of theThe CPR valve is set to limitFor CPR settings referThe suction pressure is controlled to avoid overloadingTo adjust the CPR valve, refer toNormally closed thermal switch on Standby units only. As evaporator cools to set point, the switch closes andSwitch terminates defrost by opening at predeterminedThe quench valve is a normally closed solenoid valveThe valve allowsBPT settings refer to section 1.6.2.The evaporator is of the tube and fin type. The operationAir movement over the evaporator is provided by an electric fan.The low pressure switch is a normally closed switchLP settings refer to section 1.6.2.Standby Fuse (F3) -- 5 Amp. Transformer Fuse (F4) -- 5 Amp. Clutch Time Delay Relay (CT) -- Single Phase. Only. Clutch Relay (CR). Motor Contactor (MC).
Carrier Zephyr 30s Service Manual
Overload Relay (OL) (230V Only)Rectifier Bridge Assembly (BR). Filter Capacitor (C1). Start Relay (STBR). Run Capacitor (CR). Start Capacitor (CS). Heat sink (rectifier bridge). Figure 1-5 Typical Standby Control BoxStandby Relay (SR). Figure 1-6 Standby Microprocessor ModuleFigure 1-7 Road Microprocessor ModuleOnce the set point is entered at the Cab Command,The unit may cycle the standby motor or fans unexpectedly as control requirements dictate. The control system consists of the Cab Command located in the driver’s section (See Figure 1-8) and theThe Carrier Transicold Control System incorporates theFigure 1-8 Cab CommandModelDisplacementOil ChargeApproved Oil. Mobil Arctic EAL68Automatic triggering or at preset intervals:Only). Opens at:Refer to Table 1-1.Evaporator Fan Motor (EFM). Bearing Lubrication. Factory Lubricated. Horse PowerOperating AmpsSpeed. Condenser Fan Motor (CFM). Operating Amps. SpeedVoltage. Type of Connection. PhaseAssembly. Standby compressor platform. Standby motor platform. Standby motor pulley. Evaporator fan motor. Evaporator fan. Condenser - frame. Mounting BoltsContactor DataThis is accomplished by the following fuses and safety devices. AutomaticSafety Device. Device setting. Unsafe ConditionsAutomatic reset of lowFuse on electronic boardElectronic relayFuse F3 (a)Standby fuse F2 (a)Fuse F1 (b)MicroprocessorMicroprocessorFuse FITimer 5 min. Self-protected opening. Depending on Selection. See electrical wiring diagram. Self-protected openingOpens at 30 A (12 V). Opens at 4 A. Opens at 1 AWhen cooling, the unit operates as a vapor compressionThe main components of theThe compressor raises the pressure and temperature ofWhen operating on the road compressor, the flow alsoThe condenser fan circulates surrounding air over theHeat transfer is thusLiquid refrigerant flows from theThe receiver stores the additional charge necessary forThe refrigerant leaves the receiver and flows through aThe refrigerant then flows through a check valve.
Carrier Zephyr 30s Repair Manual
TheThe refrigerant then flows through the filter-drier, whereThe refrigerantThe sight glass is fittedThe refrigerant then flowsThe liquid than enters the thermostatic expansion valveThis cold air isThe transfer of heat from the air to the low temperatureOn 115v units the refrigerant then enters theThe quench valve opens as required to maintain aWhen refrigerant vapor is compressed to a highWhen the microprocessor activates heating or defrost,The main difference between heating and defrosting isWhen the pressure is above the setting of theWhen pressure isShould a problemThe Control System consists of the microprocessorThe Cab Command includes the LCD display andThe information is accessed by keypadThe microprocessor controls the following functions:For further details on digital message display, seeThe Cab Command is mounted in the cab and allows theFigure 2-1 Cab CommandThe digital display consists of 3 alphanumericTheThe display alsoThe displayDigital Display. Standby operation LED. Road operation LED. Unit operating LED. D Green: cycling (left-hand side). D Red: malfunction (right-hand side). The driver can display the refrigerated compartmentWhen the battery voltage is too low, a fail-safe systemThe command consists of the display and the keypad. The keypad and display serve to provide user accessAfter an alarm has been present for 15 minutes, the redThe light willAt that point the steady greenUnit operating LEDsUnder normal operation, the green LED will indicate theGreen LEDSteadyGreen LEDGreen LEDThe keypad consists of six keys that enable the operatorManual defrost control key. Unit start-up keyOn road operation, the unit can also beSetpoint -differential of. Unit data and function modification keysThe display scrolls through parametersFigure 2-2 Green Light Status -- StandbyUnder normal operation, the green LED will indicate theSteady greenDecrease key for selected data.
Increase key for selected dataBefore starting the truck engine or connecting standbyIf starting unit for the first time after installation the compressor pressure regulatingInspect battery cables for signs of wear,Also check battery cable routing to ensure that clamps are secure and thatPress the ON key to start the unitFor Road units, start up is timeThe digital display of the Cab. Command displays the refrigerated compartment temperature.Check that temperature set pointIt is possible to increase or decrease the set point byIf display stays highlighted, the set point displayed hasThe new setting for the set point is validated by pressingIf the unit is to be operated in the standby mode, connectOFF key on Cab Command) and externalDisplays the set point temperature. Decrease the set pointMake sure the power plug is clean and dryValidate set point temperature. Return to display of refrigeratedPress manual defrost key toTo adjust theIf standby power isTo access the alarm messages. Shut-down unit.Press SET for 5 seconds: enables access to alarm messages. Modify parameters. Validate modified settings. Return to display of refrigeratedOnly validated changes are recorded. Table 2-1 Alarms For Road Only Units. MalfunctionCodesNo malfunction.Programming error on part of operatorMalfunction. CodesNo malfunction. Unit in operation.Programming error on part of operatorUnits. There is a 40 second time delay during start--up. AfterCab Command will display the message “bAt”. Unit willIf the battery voltage has notPress the SET key to display eepromPress SET key to return to refrigeratedThe alarm list provides information on current alarmsPress the OFF key or turn the ignitionUnit start-upUnits are configured for CelsiusSee Figure 1-6.The differential can be selected by scrolling through. Factory setting isThis feature determines whether the evaporator fan is on or off whenThe factorySET key.Shut-down unit.Modify parameters. (See a.Validate modified settings.
Cab Command reverts to refrigerated compartment temperature display and the configurationThis setting determines the length of time in minutes the unitThe defrost duration can be selected by scrolling throughSelection MUST be validated byModify parameters.The procedure for adjusting the functional parameters isUnits are configured for CelsiusModify parameters.Figure 2-4 Temperature Selection JumperThe differential can be selected by scrolling through. Factory setting isThis feature determines whether the evaporator fan is on or off whenThe factorySET key.Since all 30S units covered by this manual have aModify parameters. (See a.Validate modified settings.Cab Command reverts to refrigerated compartment temperature display and the configurationThis setting determines the time between defrosts in hours. The defrost interval can be selected by scrollingSettings are for either automatic defrost (AUT) or fixed time intervals betweenSelection MUST be validated byPress OFF key on the. The next steps must be performed with the unit ON:The unit operates in the perishable mode with set pointsFigure 3-1 Operating Sequence -- Perishable. ModeThe unit operates in the frozen mode with set points at orThis will allow liquid into the suction line in order to cool compressor. Once the discharge temperature decreasesDE--energizing the PP.If the continuous air flow parameter is set to ON, the evaporator fans will continueIf the continuous air flow parameter is OFF, the evaporatorA 5 minute delay is required before restart is allowed.The condenser fan andFigure 3-2 Operating Sequence -- Frozen ModeSection 1.8.2 for a description of the refrigeration circuitThis prevents the unitDefrost may be initiated bySection 1.6.2 for settings). In defrost mode, theThe unit may cycle the fans and operating compressorPress OFF key on the cab command and disconnectR134A and POE oil. For more information see Technical Procedure 98-50553-00 -- Inert Gas. Brazing.
Table 4-2 Service Category DescriptionsRegular servicing is required in order to optimize the lifeThe recommended scheduledTable 4-1 while descriptions of the service proceduresTable 4-2Table 4-1 Maintenance SchedulesDCut-in. Refrigerant: Type R134a. DFan shut-down. DCut-out. Road compressor oil type: The road compressors are. DDefrost water drainService C 1. Check the operation of the evaporaPAG type are strictly incompatible with the operationRefer to paragraph 1.6.1. Service D 1. Change the removable relays, fusesBeware of V-belt and belt-driven components as the unit may start automatically. A belt tension gauge provides an accurate and easyProperly adjusted belts give long lasting and efficientThe Belt Tension gauge can be used to adjust all belts. The readings which we specify for Carrier TransicoldWhen using this gauge, itNew Install. TensionRunning. TensionNm)Figure 4-3). To perform service using the manifoldR-134a cylinder. Figure 4-1 Belt Tension GaugeBelt tension depends on each kit. Refer to Installation. Instructions provided with the kit for belt tensionWhen installing a new V-belt the tension should beStandbyThe gauge set is nowCompressorFigure 4-2 Layout of V-beltThis returnsMVS--115--F--L--CT (115V) or MVS--240--F--L--CTCompressor.Backseat bothLow Pressure. Gauge. To remove the refrigerant from a compressor that is notHigh Pressure. GaugeHand Valve. OpenedHand ValveAccess ValveTo High Side. Access ValveTesting jointsManifold Gauge Set. Hose Fitting (0.5-16 Acme). High Side Field Service Coupler. Low Side Field Service CouplerEvacuate and dehydrateFigure 4-3 Manifold Gauge Set (R-134a)Installation of a new filter--drier may be performedHeat lamps or alternate sources of heat may be used to raise systemMoisture can seriously damage refrigerant systems. The presence of moisture in a refrigeration system canThe most common areRefrigerant Recovery Unit. Refrigerant Cylinder.
Evacuation ManifoldFigure 4-4 Vacuum Pump ConnectionAlso, as shown, connect a evacuation manifold, withFigure 4-4 to the vacuum pump and refrigeration unit.Close the electronic vacuumShut off the vacuumRaise system pressure to approximately 2 psig (0.14 Bar).Close off vacuumWait five minutes to see ifThe correct amount of refrigerantCorrect charge willCheck for any obstruction of the filter-drier by feeling theRemove refrigerant charge (See section 4.4). RemoveFollowing drier replacement, evacuate and rechargeSlowly open the plug on the suction andRemove the compressor from chassis.Do not use a nitrogen cylinder without aRefer to section 1.6.4 for torque values.Ohmmeter will indicate resistance if switch is closed (HP1)Figure 4-5).Pressure switch settingsWhile observing meter, slowlySlowly openCompressor oil type: The road compressors areEnsure compressor is marked with a factory stickerOils of PAGOpen pressure onReassemble the motor. Install new brushes and replace cap.It is not necessary to remove the refrigerant charge toDisconnect leads and remove coil junction box ifThis information appears on the coil voltage plate and the coilPressure regulator. Nitrogen cylinder. Bleed-off valveSwitches HP1 And HP2Remove the enclosing tube.If o-ring is toFigure 4-7 Hot Gas or Condenser Pressure. Control SolenoidVoltage plate. Coil assembly. Enclosing tubeFigure 4-6 Fan Motor Brushes. To check brushes proceed as follows:See Figure 4-6Place all parts in the enclosing tube in proper sequence in order toThis dust couldDo not use abrasiveSee Sections 4.6 and 4.7.Figure 4-9. Figure 4-8 Compressor Pressure Regulating ValveThis will ensure a suctionTo adjust the. CPR valve, proceed as follows:Refer to paragraph 1.6.2 for CPR valveThis will preventStep f. from the average temperature measured in. Step g. The difference is the superheat of the suctionFigure 4-9 Thermostatic Expansion Valve Bulb. And ThermocoupleMUST be disconnected.
Carrier Zephyr 30s Repair Manual Download
When welding is performed onThe recycled cardboard cartons create much more fiberThe fiber dustIf the coil is notDue to the ”washing” action ofAs each circuitCardboard fiber particles after being wetted and driedReverse flush (opposite normal air flow) with cleanA garden hose with sprayMake sure drain lines areRinse coil with fresh water if a detergent is used. Under no circumstances should anyone attempt to repair the microprocessor moduleAlthough there is less danger of electrical staticThis not onlyAlthough the microprocessorBar. PsigThe unit may cycle the fans and operating compressorPress OFF key on the cab command, turn vehicle engine off or disconnect power plug and open circuit breaker.Should a problem develop with the control system, contact your nearest Carrier TransicoldTable 5-1 Alarm IndicationsHigh Pressure Switch (HP1). Open (Road)Unit undercharged. Liquid line filter--drier restricted. TXV malfunction. Verify operation of evaporator fans. Failed switch. Unit overchargedHigh Pressure Switch (HP1). Open. Verify operation of condenser fan. Noncondensibles in system. Discharge check valve failed closed (standby only. Failed switchElectric motor overload. Units. Road Compressor ClutchThermal overload open in motor windings.Units. Contactor coil either high or low (0.2A for 3 phase;Verify plunger moves freely. Replace contactor. Verify motor rotates freelyReference. ParagraphVerify line voltage. Current draw of road clutch coil either high or low. Verify condition of brushes. Replace motor. Verify motor rotates freely. Replace motorUnits. DescriptionParagraph. Heating option control -- Either Verify coil resistanceCheck wiring to controls. Current draw of coil high or low (approx 1.6 amp). Hot Gas Solenoid ValveReplace coil. Current draw of coil high or low (approx 1.2 amp). Quench. ValveReplace coil. Condenser Pressure ControlUnit out of range for 15 minutesUnits. Hot gas solenoid open. Unit out of range for more than 15 minutesUnits.
Carrier Zephyr 30s Repair Manual Pdf
Heating option not active (Set configuration). Unit terminated defrost after 45 minutesUnits. Set point adjusted out of theReturn air sensor defective. Vehicle battery voltage lowLow Battery Voltage. Check alternator systemIf operating on standby, shut down vehicle engine. Err. Set point error. Programming error. Reset.CorrectCompressor drive (clutch) defective. Compressor defective. Defrost cycle has not terminated. Abnormal pressure. Refrigeration system. Hot gas solenoid malfunction (HGS1)Compressor. Expansion valve malfunction. Non--existent or restricted evaporator airflow. Compressor malfunctionHot Load. Refrigerated compartment. Defective refrigerated compartment insulation or air leak. Temperature microprocessor malfunction. DefectiveAbnormal pressure. Refrigeration. Hot gas solenoid malfunction (HGS1). Compressor drive (clutch) defective. Compressor defectiveDefrost thermostat (DTT) open or defective. Hot gas solenoid valve malfunction. Automatic defrost will not initiate. Defrost disabled through cab command. Microprocessor defective. Manual defrost will not initiate. Defrost thermostat (DTT) open or defective. Defrost cycle initiates but does. Hot gas solenoid malfunction (HGS1)Condenser Pressure Control valve malfunction (HGS2). Wet load. Frequent defrost. Defrost settings set to low. Does not terminate or cycles on. Defrost thermostats (DTT) shorted closedCondenser coil dirty. High discharge pressure. Refrigerant overcharge. Low discharge pressure. High suction pressure. Low suction pressure. Suction and discharge pressuresHigh discharge pressure. Hot gas solenoid malfunction. Low refrigerant charge. Compressor pressure regulator misadjusted (CPR). No evaporator air flow or restricted air flow. Excessive frost on coil. Hot gas solenoid malfunctionCorrectReplaceCondenser fan or HP2 pressure switch defective. Noncondensibles in systemHot gas solenoid valve malfunction. Compressor pressure regulating valve misadjusted (CPR).
Condenser Pressure Regulating valve fault (HGS2)Compressor. Condenser or evaporator fan. Loose mounting bolts. Worn bearings. Worn or broken valves. Liquid slugging. Insufficient oil. Loose shroud. Bearings defective. Fan loose on shaft. Bent shaft. TightenCheck. Check. CheckFuse open. Microprocessor malfunction. Replace. CheckHeavy frost on coil. Evaporator coil blocked. Coil dirty. Evaporator fan loose or defective. Evaporator fan rotating backwards. No or partial evaporator air flow. Evaporator air flow blocked in refrigerated compartment. Fan motor(s) malfunction. CheckCheck. ReplaceLow suction pressure with highLow refrigerant charge. External equalizer line plugged. Broken capillary. Superheat setting too highRepairSuperheat setting too low. Pin and seat of expansion valve eroded or held open byInsulation missing from sensing bulb. Low superheat setting. High superheat. Expansion valve settingNo power to valve. Improper wiring or loose connections. Valve improperly assembled. Coil or coil sleeve improperly assembled. Valve does not function properly. Movement of plunger restricted due to:Valve shifts but refrigerant. Foreign material lodged under seatDefective seatMotor contactor defective. Motor Overload open. Standby compressor fails to start Improper power supply. Fluctuating suction pressure. Standby motor starts, then stopsCheckCheck. Correct. CheckThe unit may cycle the fans and operating compressorPress OFF key on the cab command and disconnectCommand! Should a problem develop with these components, contact your nearest Carrier.